
Decoding the Data: Understanding Refrigerator, Freezer, and Incubator Performance Metrics
Refrigerators, freezers, and incubators are often the unsung heroes of scientific and medical research. Their role in maintaining precise conditions for sensitive samples and products is critical, and making the right purchasing decision can significantly impact the success of your laboratory operations.
However, understanding and comparing the performance metrics for these essential pieces of equipment is not always straightforward. Various factors, such as differences in testing conditions, unit configurations, and how data is presented, can make it difficult to interpret performance claims with confidence.
In this eBook, PHC Corporation of North America (“PHCNA”) provides a comprehensive guide to help laboratories make more informed decisions when evaluating refrigeration, freezing, and incubator systems. We’ll delve into key performance metrics, specifically focusing on Recovery After Door Opening — a crucial aspect of equipment performance that ensures the integrity of sensitive materials and the efficiency of laboratory operations.
Key Highlights of the eBook:
1. Recovery After Door Opening: The Importance and Challenges
Recovery after door opening refers to how quickly the internal conditions (e.g., temperature, humidity, CO2 levels) of a refrigerator, freezer, or incubator return to their set point after the door is opened. This performance metric is vital for preserving the integrity of stored materials, whether it’s vaccines, cultures, or reagents. However, recovery data can be tricky to interpret due to:
- Variation in Testing Conditions: Different manufacturers may test under varying environmental conditions, such as ambient temperature, humidity, and air pressure, which can lead to discrepancies in performance results.
- Temperature Probe Placement: The location of temperature probes inside the unit can influence the reported recovery times. Probes near cooling sources will return to set temperature faster than those placed further away.
- Inner Door Configurations: Many freezers, particularly ultra-low temperature (ULT) models, have multiple inner doors that help maintain internal stability. The number of doors opened and how long they are left open can significantly affect recovery times.
- Unit Filling: The more a unit is filled, the faster it can recover after a door is opened. Testing on empty units is common, but this may not reflect real-world conditions if your unit is routinely filled with samples.
2. Variation in Data Reporting: Product Families vs. Individual Units
Another challenge when evaluating performance data is understanding whether the results provided apply to the entire product family or only to a specific model. Many manufacturers report recovery data for a range of models within a product family, but this data may not accurately reflect the performance of each individual unit. It’s essential to check whether the data is specific to the unit you’re considering or if it’s an aggregate result that might not apply to your exact needs.
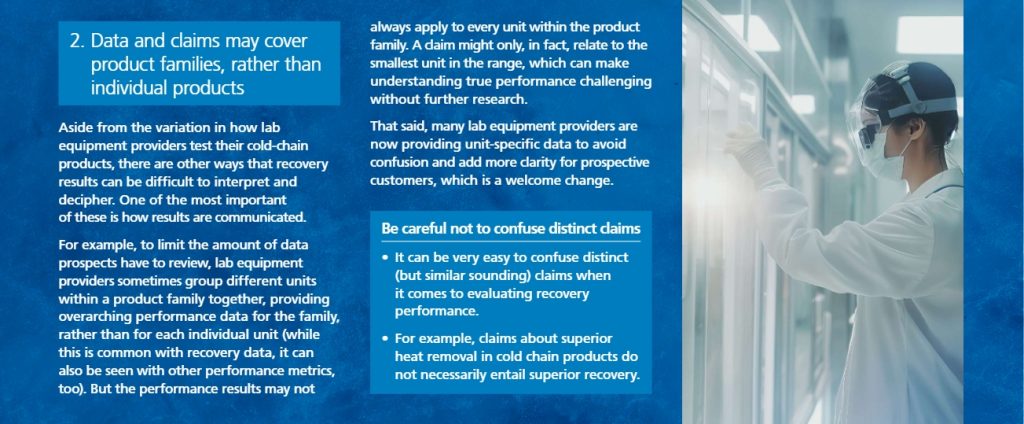
3. Evaluating Incubator Performance Metrics
While refrigerators and freezers have their own set of challenges, incubators introduce additional complexities due to the multiple factors that can impact recovery:
- Door Opening Duration and Speed: How long the door is open and how fast it’s opened can significantly affect recovery, especially when it comes to controlling CO2 and humidity levels.
- Ambient Temperature and Airflow: The testing environment’s temperature and air circulation can vary, which in turn can influence how quickly an incubator returns to optimal conditions.
- Traffic in the Testing Space: Movement in and around the incubator, such as researchers walking by, can disrupt internal conditions, which may not be captured in testing conducted in isolated settings.
4. Key Recommendations for Making Confident Purchasing Decisions
To make informed purchasing decisions, laboratories need to consider the following:
- Understand Testing Conditions: Pay close attention to the testing conditions used by manufacturers, including ambient temperature, door opening duration, and the placement of temperature probes. Compare these to your lab’s typical conditions.
- Look for Unit-Specific Data: Ensure that the performance data corresponds to the exact model you’re purchasing, not just the broader product family.
- Clarify Performance Claims: Be cautious of terms like “superior heat removal,” as they may not always equate to better recovery performance.
- Use Real-World Simulations: Whenever possible, conduct in-lab testing or simulations to see how the equipment performs under your lab’s typical operating conditions.
5. The ENERGY STAR® Certification Advantage
For refrigerators and freezers, the ENERGY STAR® certification can provide a helpful benchmark for performance, especially when comparing models from different manufacturers. However, while it standardizes energy efficiency and certain recovery metrics, it’s important to remember that this certification doesn’t cover incubators and might not always reflect real-world performance in your specific lab environment.
This article is posted at phchd.com

Please fill out the form to access the content